The latest formulation approaches for counteracting drug solubility, stability and bioavailability issues

What kind of enhancement solutions do CDMOs need to offer their pharma clients to address pressing issues such as bioavailability, solubility and stability of their products? A recent CPHI webinar sponsored by Adare Pharmaceuticals delved deep into the issue...
While the road to market authorisation for any drug is full of obstacles, it is fair to say that a large proportion fall by the wayside due to issues with bioavailability, solubility and stability. As a result, contract development and manufacturing organisations (CDMOs) that can display a track record in providing enhancement solutions for all three of these crucial challenges are likely to steal a march on their competitors.
In a recent CPHI Webinar sponsored by Adare Pharmaceuticals, industry experts discussed the latest formulation trends and examined in some detail the current approaches for counteracting the age-old problems of drug solubility, stability and bioavailability.
A survey of webinar listeners revealed that 42.2% of respondents regarded bioavailability as their main formulation challenge followed by drug stability (28.1%) and drug solubility (20.7%).
During the webinar, Dr Nathan Dormer, Director of Drug Development, Adare Pharma described bioavailability as the entire ‘snapshot’ of the whole formulation process: “It’s not just the very technical things such as the solubility and permeability of the drug, it’s your whole dosage form design, the thought that goes into that and how it performs in the disease state and in the specific patient. And then once it takes effect in the tissue site of interest, it’s about how is it metabolized, how is it excreted and what essentially are the outcomes for the patient as a person and as a clinical treatment plan.”
For generics producers to take full advantage of their pricing advantage over branded medicines, they need to address bioavailability and solubility challenges as they must ensure that their products achieve bioequivalence, said Dr Rashmi Panda, Deputy General Manager, Mankind Research Centre.
“The major trait affecting bioequivalence is low solubility; 40% of new chemical entities that are coming have low solubility and bioavailability as well,” he said. “There is a need to enhance poor solubility and permeability of APIs to improve bioavailability and lead to bioequivalence as well.”
Dr Dormer of Adare added that while through advances in technology, it is much easier to extend drug release, difficulties remain in speeding up the action of some of these drugs and making them more bioavailable: “So we have to rely on multiple drug formulation and drug delivery techniques to meet this goal to be able to better serve our patients.”
What is immediately apparent is that there is no one-size-fits-all approach to solving bioavailability challenges and decisions during formulation design are usually based on a rigid evaluation of a specific compound’s physical and chemical properties, and its intended site of action.
On top of this, amorphous solid dispersion (ASD) technologies in manufacturing have emerged as a promising formulation approach that can improve solubility, dissolution rate and bioavailability of poorly water-soluble drugs.
Dr Dormer said that for many years, formulators have been faced with competing priorities; in other words, deciding which scenario is more important to avoid, a patient not taking a bad-tasting drug or the drug not reaching full effectiveness because of attempts at taste-masking.
“The most important thing is that the patient gets the dosage form but oftentimes that still does not work,” he said, adding that with solid and amorphous dispersions, desirable outcomes in both cases can be achieved.
“ASDs are a way we can achieve both of these metrics by being able to encapsulate the drug but also not harming the overall bioavailability,” he concluded.
One such technology very much in vogue is HME, the process of applying heat and pressure to melt a polymer and forcing it through an orifice in a continuous process. While HME came to prominence in the plastic industry to produce polymer products of uniform shape and density, pharma has now firmly latched on to the technology to mix active pharmaceutical ingredients (APIs) with polymers.
Also speaking in the webinar, Dr Feng Zhang, Assistant Professor, Pharmaceutics Department, at the University of Texas at Austin said there is a need to rationally approach formulation and process design of HME via simulation and modelling.
“I think for HME there is still too much trial and error and there should be a more rational approach,” he said. “If I know the drug and the polymer, how do I design my process? Or something can be as simple as if I have a drug and a polymer, can you tell me if HME is even feasible? That has to be done with a good understanding of the somewhat dynamic principles and the simulation and the modelling of the extrusion process.”
To listen to the webinar and learn more about the latest formulation and manufacturing technology innovations in bioavailability, solubility and stability enhancement including a case study on Ritonavir, click here.
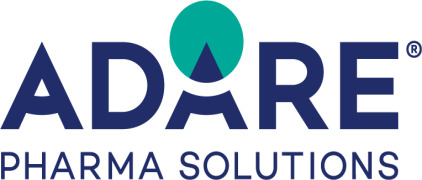
Recently Visited
Position your company at the heart of the global Pharma industry with a CPHI Online membership
-
Your products and solutions visible to thousands of visitors within the largest Pharma marketplace
-
Generate high-quality, engaged leads for your business, all year round
-
Promote your business as the industry’s thought-leader by hosting your reports, brochures and videos within your profile
-
Your company’s profile boosted at all participating CPHI events
-
An easy-to-use platform with a detailed dashboard showing your leads and performance