ColdPound™
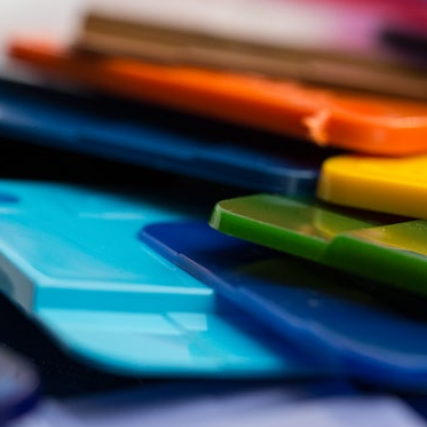
Product Description
Americhem Healthcare

-
US
-
2024On CPHI since
-
2Certificates
Company types
Primary activities
Americhem Healthcare

-
US
-
2024On CPHI since
-
2Certificates
Company types
Primary activities
More Products from Americhem Healthcare (5)
-
Product ColorRx®
ColorRx® pre-colored medical compounds are specially created with precise properties and biocompatible resin technology to achieve exact processing requirements and product expectations. -
Product EcoLube™
EcoLube™ line of PFAS-free internally lubricated compounds delivers advanced tribological and mechanical properties in moving plastic parts and addresses industry challenges around proposed PFAS regulations. -
Product InElec®
InElec® compounds incorporate conductive technologies including additives, fillers, and fibers to impart various levels of conductivity to inherently insulative base resins. -
Product InLube®
InLube® internally lubricated compounds and alloys are specially designed to help mold manufacturers reduce the friction of moving plastic parts and improve their wear resistance. -
Product InStruc®
InStruc® line of reinforced plastics can be used in any application that requires increased strength, stiffness, heat resistance, creep resistance, fatigue endurance, impact protection and dimensional stability.
Americhem Healthcare resources (3)
-
Brochure ColorRx® Products
WHERE COLOR MEETS COMPLIANCE Our products are tailored to meet color, performance, and compliance standards in the highly regulated healthcare market. -
Brochure Americhem Healthcare launches ColorRx® medical grade polymers in Europe
European medical device manufacturers and stakeholders can benefit from local production and world-class ISO 13485 quality. Americhem Healthcare, a globally rec
Frequently Viewed Together
Recently Visited
Position your company at the heart of the global Pharma industry with a CPHI Online membership
-
Your products and solutions visible to thousands of visitors within the largest Pharma marketplace
-
Generate high-quality, engaged leads for your business, all year round
-
Promote your business as the industry’s thought-leader by hosting your reports, brochures and videos within your profile
-
Your company’s profile boosted at all participating CPHI events
-
An easy-to-use platform with a detailed dashboard showing your leads and performance